Recent advances in its in-house developed robotic technology has enabled Cama Group to further enhance its machine portfolio, with a solution designed to address some of industry’s most pressing concerns in terms of smaller packaging sizes and available plant real estate.
At the heart of many of Cama’s machines are its robotic solutions. Developed in-house to cater for the precise needs the packaging industry, this robotic technology sets Cama apart from other suppliers, giving it the capability to offer far greater performance, accuracy, consistency and repeatability than many other machine suppliers. Thanks to significant research and development efforts, a new smaller, faster variant of its robotic solutions – in conjunction with an innovative approach to its phasing conveyors – has given Cama the opportunity to reinvent the capabilities of its popular IF range, with the introduction of the new IF320 monoblock machine.
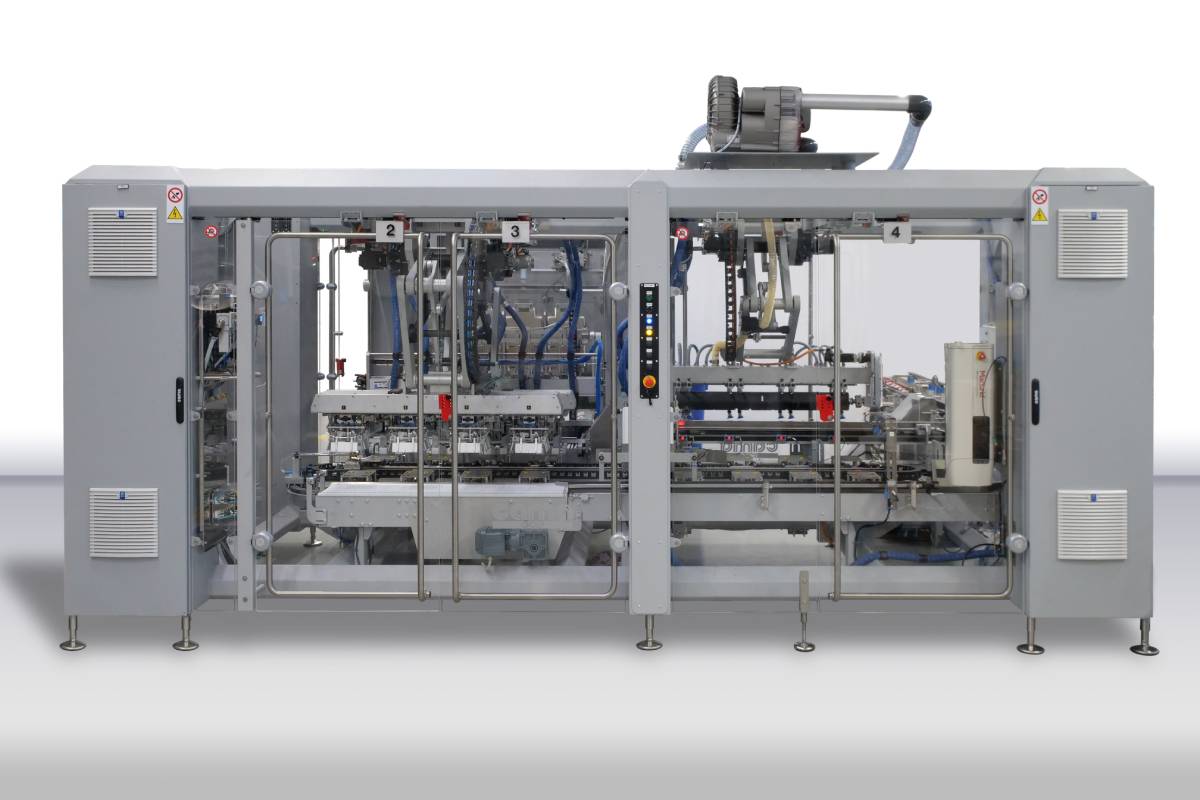
Francesco Riva, Sales Engineer Director at Cama explains: “These new technologies have been under development for a while now and are key to helping us address a major demand from our global customers. They are looking for broader capabilities in the small-to-medium-box packaging segment as end consumers migrate towards smaller portion sizes, not just because of demographic changes, but also to reduce waste from unused products supplied in larger formats. Key to the evolution is the new-format robot we have created. Not only is it faster, but its smaller installed size means it can be clustered closer to other robot base units. This means we can shrink the overall size of the machine and, just as importantly, change its shape to match available real estate and product flows.” Hand in hand with the new robot is a new design of phasing conveyor. “A typical box-forming, robot loading, and box-closing machine is linear, with a vertically mounted phasing conveyor. But by laying the phasing conveyor on its side – but still using the topmost face – we create a horizontal track within the envelope of the machine that can be exploited from two sides. New carriage designs take this new flexibility to another level too. By using pneumatic ‘suckers’ or specially designed grippers instead of fixed, carton-specific lugs, we can supply platens/carriages that will cater for a variety of carton sizes without the need to replace or re-engineer them between batches. We have also the vacuum on board feature that hold the boxes and avoid format change.”
Operationally, the packaging stages are the same as with the company’s very popular IF318 monoblock packaging machine. Boxes are formed, placed into/onto the phasing conveyor, robots then pick and place the products before the boxes are closed and sealed. In the new IF320 these stages occur in a loop as opposed to a line, and because of this layout, a ‘spare’ or ‘empty’ station is created within one quadrant of the machine.
“This is where the flexibility really shines through,” explains Riva. “We can populate this empty quadrant with existing packaging stages to match the layout or infeed of the existing plant, or we can add supplemental processes, such as printing or leaflet insertion, without increasing the overall envelope of the machine.”
At just 5.2 m long, the IF320 is 30% shorter than equivalent machines, but can still offer a throughput of up to 75 boxes per minute, depending on the box size and the dynamics of the products being packaged, while quality levels and forming, closing & glueing precision are just as high as with other Cama machines.
“Thanks to this combination of robots, conveyors and expandable capacity all optimizing the in-machine real estate,” Riva concludes, “we can deliver modular solutions that can be tailored to match the precise needs of the customer applications – be it speed, space, accessibility or, indeed, special/supplemental processes.”
The IF320 takes advantage of Cama’s Breakthrough Generation (BTG) concept too, which sees modular, scalable frameworks that offer easy entry and access, coupled to a hygienic machine design. Within this framework, contemporary automation solutions, including advanced rotary and linear servo technology, is tightly coupled to the robot, to deliver the all-important flexibility and adaptability required by modern packaging operations. This machine is cross categories: can be applied to cosmetic industry, personal care, home care, confectionery, bakery, coffee, dairy…
Finally, the machine also benefits from Cama’s Industry 4.0 offering, which makes operator training, machine interactions and maintenance routines simpler, thanks to immersive augmented reality (AR). And to keep uptime to an absolute maximum, it exploits Cama’s ‘toolless’ RFID-managed changeover solution, which results in some of the fastest batch-swap/re-engineering routines in the industry.